Nearly finished automobiles awaiting chips, congested ports with cargo ships idling for weeks, and warnings of product shortages for the 2021 holiday season: these are scenes from the latest chapter in the story of supply chain volatility that has persisted throughout the pandemic, causing extreme pressure on transportation costs and timelines. This volatility, along with latent consumer demand, tariffs, geopolitical concerns, and risk mitigation around climate change and natural disasters, has caused firms to consider restructuring their supply chains for long-term resiliency. Consequently, U.S. manufacturing reshoring, foreign direct investment (FDI), and domestic expansion are all accelerating.
The domestic advanced manufacturing sector is the primary beneficiary of this growth as the number of firms and jobs in this sector proliferate; 60.5% of all new domestic manufacturing establishments to emerge between 4Q 2019 (pre-pandemic) and 1Q 2021 were in advanced manufacturing industries. According to the Reshoring Initiative, reshoring and FDI-driven job announcements are projected to reach a historic high in 2021 of 220,000, representing an increase of 38.0% from 2020. The transportation equipment industry registered the most job announcements, largely due to electric vehicle battery production, and the computer/electronics industry experienced the largest job growth year over year, with semiconductor/chip investment leading the way. These are sectors of manufacturing overwhelmingly localized in Asia, and therefore roiled by oceanic freight cost increases and shipping delays among other catalyzing factors. Two companies, TSMC and Samsung, produce close to 100% of the global supply of advanced chips, with most of the production occurring in Taiwan. Both companies have recently made or are exploring major U.S. manufacturing investments. While these high-profile project announcements have grabbed headlines, there is a widespread increase in domestic manufacturing capital expenditures across a myriad of advanced manufacturing sectors. These sectors also stand to benefit from reshoring, FDI and domestic project investment, particularly those most impacted by disrupted global trade patterns during the pandemic.
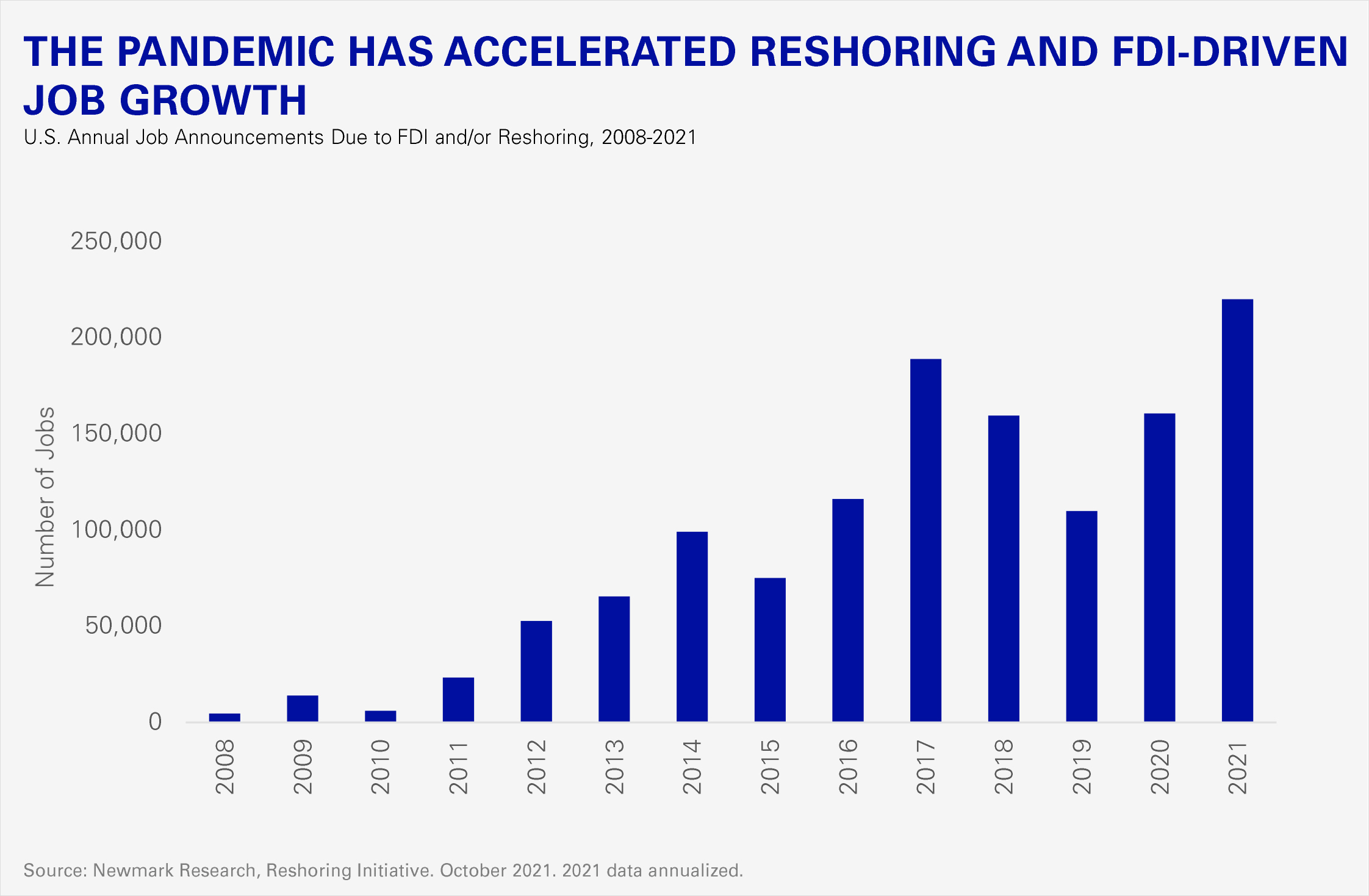
Manufacturers that depended on a just-in-time supply chain paradigm are adjusting to a just-in-case model; in doing so, some are moving the point of production closer to the point of consumption in an effort to reduce costs and disruption. The global supply chain, an intricately delicate network spanning from the planning and initial sourcing of raw materials to the delivery of the final product, often involving multiple countries and shipping methods, can take years to change and is cost-conscious. Some firms doing business in the U.S. may also increase near-shoring to closer countries such as Mexico, to develop a more resilient domestic supply chain at a more affordable cost. The shift to a just-in-case supply chain model will be additive, requiring additional U.S.-based industrial real estate demand for mining, manufacturing, warehousing and distribution. Secondary markets are particularly poised to benefit thanks to stronger population growth, lower real estate costs and larger availability of existing space and land on which to build. A focus on fostering education and skills in the increasingly automated advanced manufacturing sector will be a critical differentiator for U.S. markets looking to be a destination for foreign manufacturing investment, domestic expansion and reshoring.
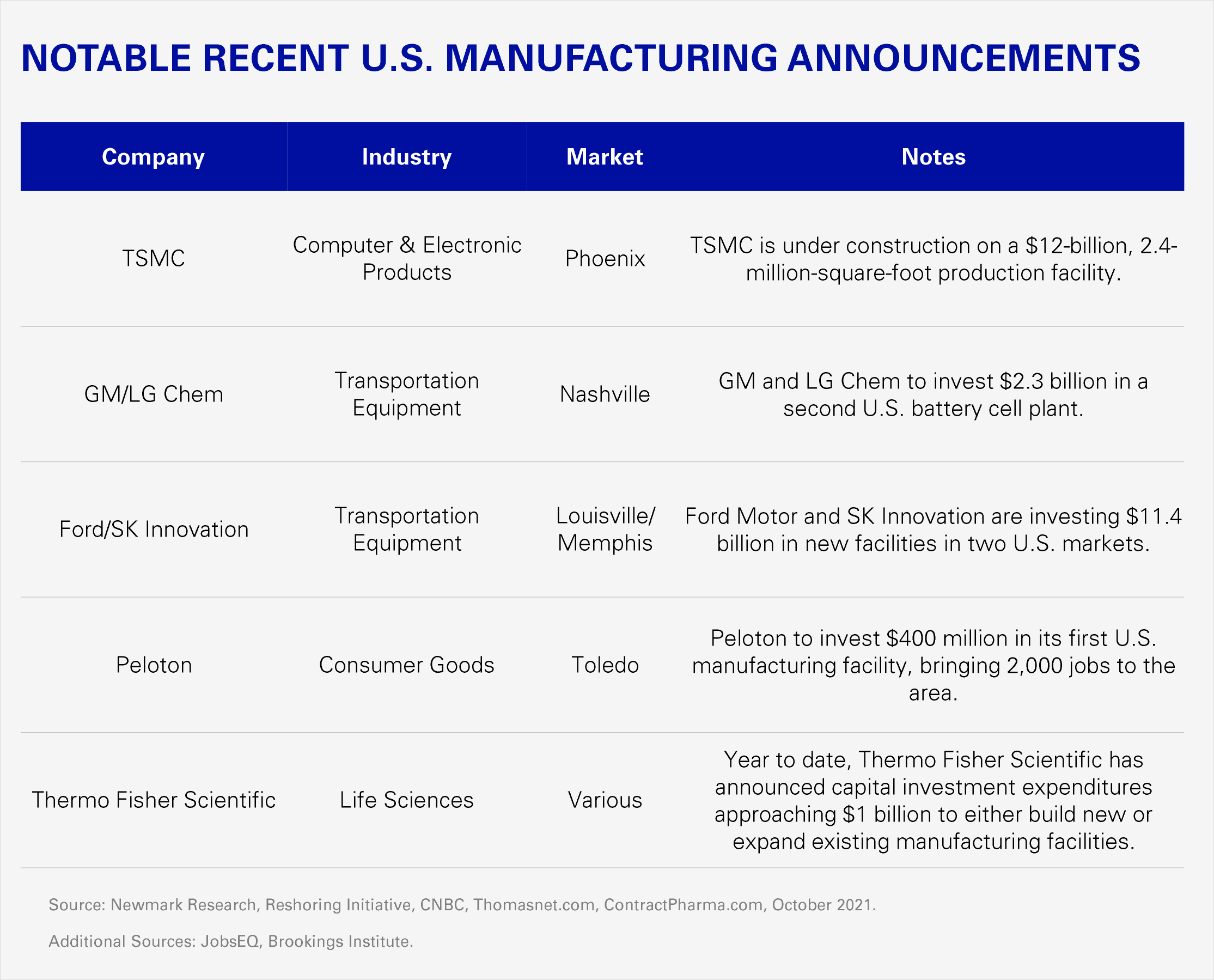